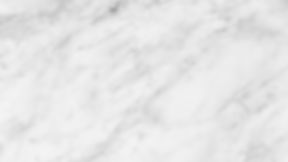
MICHAEL BAKER BUILDING
PENN STATE BEAVER, PA
HONG JIE CHEN | SENIOR THESIS
ARCHITECTURAL ENGINEERING | CONSTRUCTION MANAGEMENT
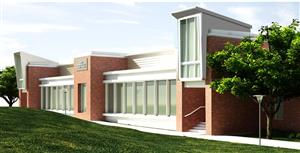
Building Statistics
Part I: Project Background
General Building Data
Building Name:
Project Location:
Building Occupants:
Size (Square Feet):
Number of Stories:
Dates of Construction:
Project Delivery Method:
Michael Baker Building
Penn State Uhniversity Beaver Campus, PA
Penn State Students and Faculties
26,200 GSF
Two Stories with a Mezzanine Level
May 11, 2015 - May 31, 2016
Construction Manager at Risk with a GMP Contract
Project Team
Michael Baker Building

Penn State Beaver

Jendoco Construction

Stantec Company
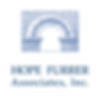
Hope Furrer Associates

LaQuatra Bonci Associates
Architecture
Michael Baker Building (built in 1968) is currently under renovation in Penn State Beaver Campus, PA. The building provides laboratory and class spaces for students/faculties of the Engineering, Science and Communication schools. The renovation work has been phased into two main parts. Phase one would include the construction of an organic chemistry lab and and the renovation of the first floor bathrooms & corridors. Phase two would focus on the renovation of the rest of the building, including the addition of an passenger elevator and two bathrooms on the ground floor. The primary purpose of this renovation is to upgrade the building system to meet current ADA and building codes, and to provide a better teaching/studying environment for staudents and faculties.

Picture source: Penn State University
International Building Code (IBC) 2009 |
National Fire Protection Association (NFPA) 13-14 | New York Building and Fire Codes
Pennsylvania Fire Code | PSU Standards
National Electrical Code (NEC) | National Electrical Safety Code (NESC)
Beaver County Zoning Code, PA
Not Applicable
Code Requirements:
Zoning Requirements:
Historical Requirements:
Building Enclosure
Following Section Drawings source: Jendoco Construction
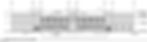

The existing building exterior is composide of brick veneer and curtain wall system. The Renovation will include the demolition of all the building exterior windows and some of the exterior bricks to install newly designed large curtain wall system. The demolition focuses mostly on the middle of east and west faces of building exterior (Figure D1 & D2). The exterior walls at the ground level of the building are CMU walls with brick veneer (Figure S1), most bricks removed from the existing building will be reused during construction (S2). Most curtain walls will be on the first level, since the west-side ground-level-walls are mostly underground. The curtain walls system will expand the opennings on the wall, providing the building interior more light and openness feeling (Figure S3). There are three parts of the building corridor system separated the building into four sections. The main entrances of the building will be extruding out on the east side of the ground level (Figure S4).

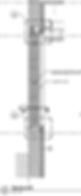
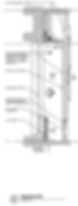

Roofing
The existing roofing system consists of a built-up roofing system providing profecient insulation and drainage protection. The existing roof of the building will be remained in the renovation, but all the mechanical and most of the insulation system will be updated in this project. Opennings will be made to allow duct work of the mechanical system. One focus on the roofing is the shadow box head above the main entrances. Lots of continuous EPDM waterproofing mambrane will be utilized in the system to provide proper insulation and protection (Shown on the Fiure right).


The renovation will include the installation of new tapered insulation roof with rubber mambrane on top of the mechanical roof level. Some wing walls will be build on roof top with same insulation (shown on the left).
Sustainability Features
Sustainability was one important idea in this project since it's an Penn State University project. The design and renovation of the building were required to meet the Penn State OPP Design and Construction Standards besides meeting the general sustainability requirements on the building codes. Many of the materials used in the construction will be recyclable material. The mechanical system is designed to preserve energy and reduce wastes in the building.
Part II: Engineering System
The renovation of the building is consisted of two phases: the renovation of the organic chemistry lab and part of the first floor as Phase I; the renovation of the rest of the building as Phase II. On each phase, the renovation process includes three main stages, including demolitions, constructions and finishes. Phase I will start a bit earlier than Phase II, and it needs to be substantially completed and open for the Spring of 2016 School Semester. The whole renovation is expected to be completed at the end of May 2016.
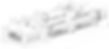
Construction
Demolition
There will be a lot of demolitions in this project, because the systems in the building will be completely updated. Some floors will be demolished and replaced with floorings for different needs, most of the windows in the building will be replace. Some of the entrances of the building will be expanded. A large part of the building façade masonry will be demolished, but some of the bricks will be reused.
Structural
The building is a 2-story cast-in-place concrete structure with mezzanine spaces. Half of the ground floor will be under surface of the ground. There are three mezzanines speces in between the main spaces of the building. Most of the foundation framing will be remained. The Roof of the building will be replaced. One thing important in this project is the addition of the elevator, which will be at the North West part of the building. An 8” CMU reinforced elevator shaft wall would be constructed.
Mechanical
A key to completing this project is the construction of an organic chemistry lab, which would be one whole phase of the project. This lab would require a lot of complex work in the process, as it requires most of the existing mechanical system to be updated. Most of the HVAC duct work will focus on the new lab areas, and most of the exhaust fans will be located on top of the mezzanines level roofs. An air handling unit is located on the roof serving for the ventilation of the building. Its supply air flow capacity is 15400CFM. The building uses electric unit heaters to heat the interior, two split system A/C units cools the building.
Electrical & Fire Protection
Electrical power will be provided to the building through an existing 23KV Campus Transformer, which supports other Beaver campus buildings. Sprinkler system will be updated and fire insulation is emphasized in the construction.